Brace yourselves! This blog entry is VERY educational. 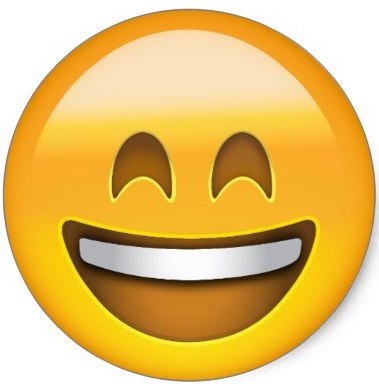
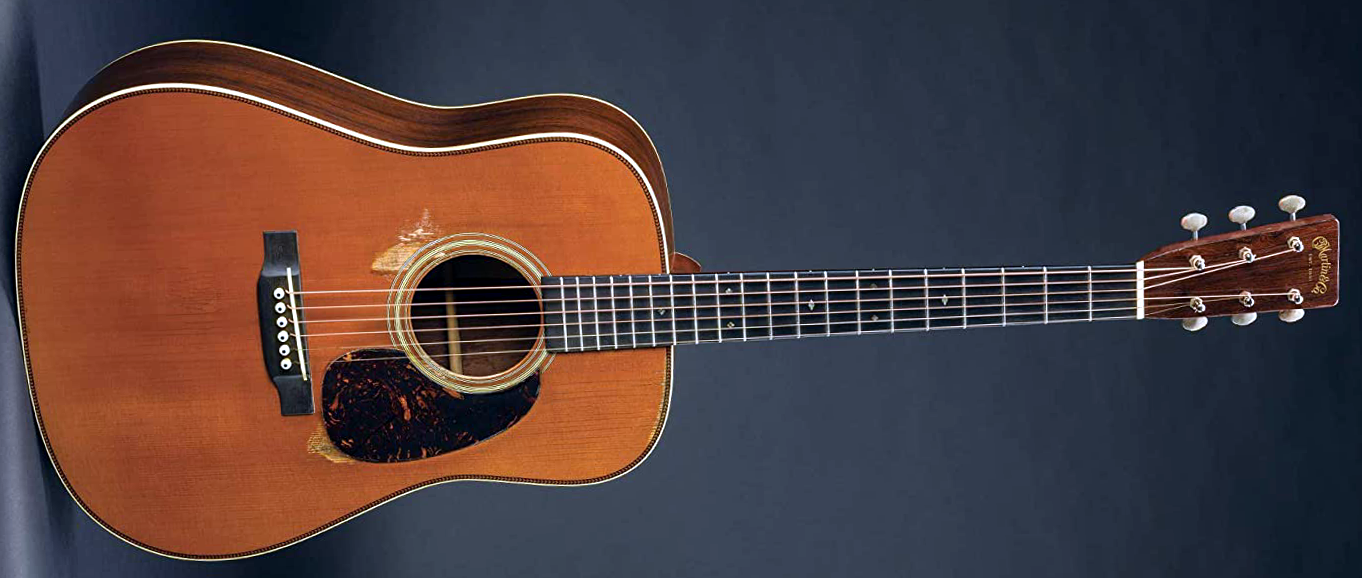
The D-28 Authentic 1937 Aged has authentic scalloped forward-shifted X-bracing
The terms “X-bracing,” “forward-shifted bracing,” and “scalloped bracing” are encountered all over the internet and often mentioned by Maury when discussing Martin guitars. But many people do not understand what these terms actually refer to and why they matter when it comes to the sound production of an acoustic guitar. And since Martin simplified their public spec sheets in recent years, there is even less information on their website concerning the details of what bracing is being employed to make their many different models.
So, we felt it was high time we devoted another blog post to the different types of bracing used on Martin Guitars, as there have been significant changes since our last bracing post almost eight years ago. We will approach this topic by looking at the different “series” that Martin uses to categorize their main models, such as the X Series, Road Series, and Standard Series. But first, let’s examine the basics of bracing, and explain what is meant by the terms “scalloped bracing,” forward-shifted bracing,” and “X-bracing.”
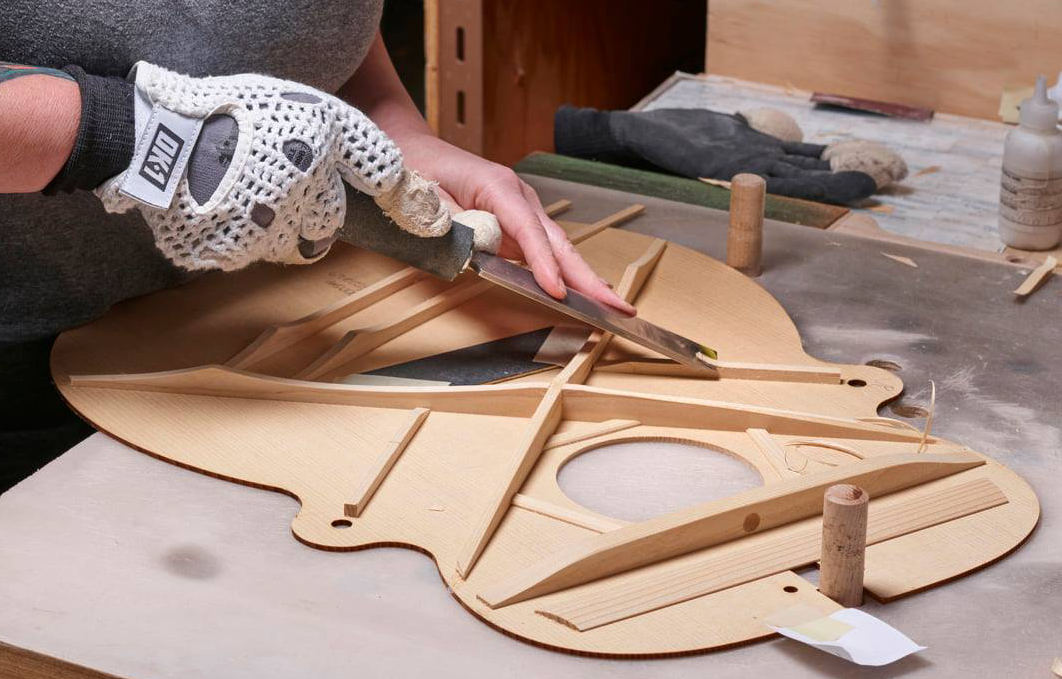
What Exactly is Bracing Anyway?
Bracing can be thought of as the wooden framework around which a guitar is built, not unlike the frame of a house or a vintage airplane. But unlike a Sopwith Camel, the bracing we do not see behind all that pretty tonewood has a great deal to do with the sound being made by that musical instrument, and how nicely it makes it.
The best guitars are those built to optimize tone production without compromising the instrument’s structural integrity. That is no easy feat, if it is to be done as expertly as they do it at C. F. Martin & Co.
Durability
The moment a steel string guitar is tuned up to concert pitch, its body and neck are brought under tremendous tension, with up to 190 lbs. of stress acting upon a guitar that weighs less than 5 lbs.. Golly!
The guitar’s bracing – those thin, raw, unfinished strips of wood – is all that keeps that beautiful musical instrument from collapsing into a heap of junk, as the string tension continuously pulls on the top 24 hours a day, in an effort to rip it from the sides and curl it toward the neck like the lid of a sardine can. And the beautiful wood that makes up the back is forever trying to roll itself up and turn back into a tree.
It would be easy for any woodworker to reinforce the back and top of a guitar, if stability were all that mattered. But a luthier’s skills are tested to their limit, because a guitar only sounds good if the wooden body is allowed to vibrate as freely as possible, which is very difficult to achieve, if the instrument is to remain intact for years or decades.
Guitar bracing is made up of struts, technically speaking. They operate like the struts on an aircraft that provide the needed support for the wing, while allowing the wing the flexibility to absorb or resist stress so it can do its job of riding the airwaves and keeping the plane aloft. The struts of a guitar must support its back and top while also providing the flexibility required for tone production, while controlling and aiding in that flexibility as needed.
Back bracing is relatively simple. Its purpose is to stabilize the very thin plates of tonewood, while allowing them to respond to the soundwaves striking them. The exact size, shape, and layout of back bracing was determined through experimentation over the years, and fine-tuned for the specific body sizes.
The struts supporting the top are another matter. That is where the sound comes from. That is why the technical name for a guitar’s top is the “soundboard.” And the luthier must install the bracing necessary for durability while also achieving the least amount of bracing possible to insure maximum resonance. As C. F. Martin IV put it, “The best tone is achieved when a guitar is built so that when you play it, it is almost about to explode, but doesn’t.”
Tone Production
The kinetic energy created by playing the strings gets transferred to the top, which begins to vibrate so that it generates soundwaves that enter the sound chamber. The dimensions of the sound chamber are determined by the size of the back and sides, which also reflect the soundwaves, increasing volume and bass response, while adding tonal coloring to the sound as well. The larger the sound chamber, the louder and bassier the musical instrument. But the bracing also has considerable influence on these and other facets making up the audible tone of the guitar. Again, this is all easier said than done.
Not all flattop steel-string guitars are created equal. But every one of them has a bracing pattern that is based upon of the ingenious acoustic guitar bracing that was invented by Christian Fredrick Martin sometime before 1845. It is known to the world today as “X-bracing.”
X-Bracing
X-bracing gets its name from the largest brace, which is actually made of two struts known as “cross braces” that are connected where they intersect; this creates an X shape centered between the sound hole and bridge plate, near “waist” of the guitar, where the smaller upper bout and the larger lower bout meet. The cross braces fan out to support both bouts, while leaving a wide expanse across the center of the lower bout.
The vibrating energy from the strings enters the soundboard through the saddle, embedded in the bridge, and the bridge plate inside the guitar. From there, the energy spreads out and quickly enters the X brace, which then channels it out across the entire top.
Other types of support are added around the X brace, usually in the form of smaller struts. In terms of tone production, the most important of these are the “tone bars,” set at an angle across the lower bout, between the two opposing arms of the X brace.
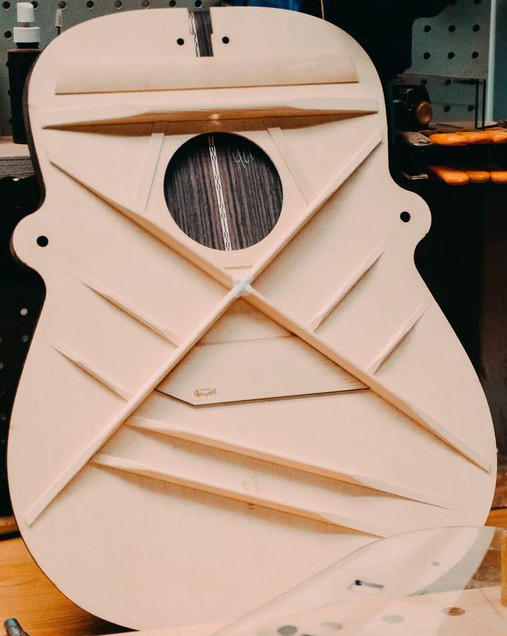
Martin-invented X-bracing rules the guitar world
The exact size and shape of the X brace and the tone bars will differ, depending upon the specific instrument, as Martin enhances or attenuates certain characteristics that make up the voice of a guitar. This and other detailing is evolved in the various types of X-bracing found on today’s many Martin models. Some are based on the body size, others by the specific series and price range.
The earliest surviving example of a guitar with an X brace was built by C. F. Senior in 1843. That little parlor guitar with its gut strings is still playable today, and sounds absolutely lovely. From across 178 years since its creation, it sings an aria in testament to the durability and tone enrichment that comes from supporting a guitar’s soundboard with X-bracing.
Martin’s X-bracing turned out to be perfectly suited for the steel guitar strings that came into use in the early 1900s. In the 1930s, Martin introduced the world to the first 14-fret acoustic guitars created specifically for steel strings. These included the two most popular body sizes in history, the big, bassy Dreadnought and the Auditorium size used for the OM and 000 models, with their balanced tone across all six strings. These and other classic designs are found throughout all of Martin’s instrument series today. And all of them have X-bracing.
Forward Shifted Bracing
Sometime in the 1970s it was discovered that Dreadnoughts built before 1939 had their X-bracing in a slightly different position than those built afterwards. There are no company records to explain why this change occurred. But Martin later determined that this difference is partly why their guitars from the 1930’s have a richer tone than those made in later decades.
The phenomenon is caused by moving the main X brace away from the bridge plate, approximately 1 inch closer to the sound hole. This widens the struts of the X brace on either side of the bridge plate, allowing that area to have greater flexibility when infused with the same amount of vibration. And the flexibility of the entire lower bout is similarly affected. This results in a voice that can be characterized as throatier and with greater bass response.
Martin first re-introduced this X brace positioning on the Vintage Series instruments of the 1990s. When it became obvious that more and more custom orders were requesting it, Martin brought forward-shifted bracing into the Standard Series, beginning with the D-18 in 2016 and the D-28 in 2017. These throatier, bassier versions of Martin’s most popular models were an immediate success.
In 2018, Martin converted all Standard Series guitars with a top wider than the 000/OM models to forward-shifted X-bracing. In addition, they made scalloped bracing a feature on all Standard Series models, with two important exceptions, mentioned later in this blog post.
Scalloped Bracing
Beginning in the 1970s, Martin re-introduced scalloped bracing, another of C. F. Martin Sr.’s innovations from the 1840s that had been discontinued in the 1940s. It has since become a nearly universal feature on Martin guitars made today.
Scalloped bracing refer to how certain braces are shaped to have particular kinds of influence on the sound of the specific guitar. The “scallops” are actually curves that are scooped out of the tone bars and portions of the X brace, which result in long troughs where the strut has very little depth, and narrower high points where the strut is at its greatest depth and the greatest stiffness. This gives the tone bars a silhouette similar to the towers and sloping cables of a suspension bridge.
Non-scalloped bracing also gets its own particular shaping. But the result of scalloped bracing is carefully increased flexibility at certain locations across the entire soundboard.
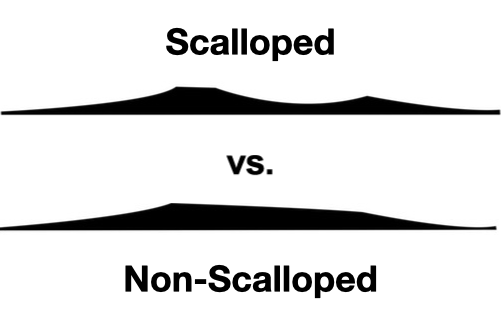
Scalloping increases brace flexibility
In terms of tone, the greater flexibility increases and extends the resonant frequencies. This means the soundboard continues to vibrate longer, creating a complex tone with a subtle natural reverb effect added to the voice of a guitar.
While the deeper sections of the bracing between the scallops maintain the structural integrity of the top, the exact location of those peaks between the troughs act as dampening nodes, which manipulate specific frequencies. Their effect is not unlike pulling down particular bands on an equalizer that adjusts the tone of your home stereo system. What makes for a good guitar and what makes for an exceptional guitar is found in the smallest details. You get what you pay for when it comes to the tone and durability of a Martin.
There are many factors involved in the bracing of a given Martin model. The difference between inexpensive, over-built guitars and the refined musical instruments making up the smallest percentage of world-class, professional-level musical instruments is enormous. Like everything about a Martin guitar, it is more than worth the price to own such an exquisite tone machine.
Martin Bracing Patterns in Use Today
The following is meant to help you make educated choices about which Martin guitar is perfect for you and your budget. We sincerely hope it helps.
Please keep in mind that Martin adjusts its specs from time to time in an effort to continually improve their product range. There may be exceptions to what you are about to read and everything is subject to change as time goes on. Some known exceptions are listed at the end of each series.
X Series Bracing
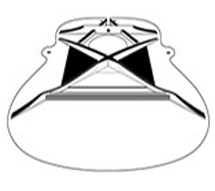
X Series “X” – This special bracing is designed specifically for soundboards made from High Pressure Laminate (HPL.) It has a main X brace that is pre-shaped to have tapered ends and a raised tone node in the bottom bout struts similar to that used on scalloped braces.
Between those two nodes is a single U-channel brace made of solid carbon fiber. This brace aids in tone production.
Two plates of High Pressure Laminate are glued to the top on either side of the X brace, shaped to fit against the struts, so they look somewhat like a bow tie. Their purpose is to strengthen the top near the waist of the guitar.
Running from either side of the sound hole are the two small braces that create an A-frame shape by running through the large cross brace above the sound hole (known at Martin as the “#1 brace” or the Traverse Bar.) These A-frame braces are an integral part of the Mortise & Tenon neck joint assemblage, helping to stabilize the connection of body and neck, while also transferring some vibration from the neck to the soundboard.
Our good friend Aaron Short of Aaron Shorts Music told us just a week ago how impressed he was when he heard the DX Johnny Cash model, which has X Series “X” bracing. And he is now thinking of purchasing one for his eclectic stable fine guitars. If you have never experienced Martin’s X Series guitars and ukuleles for yourself, we encourage you to do so. They have a very satisfying, musical tone for the least amount of money that gets you the legendary Martin name on the headstock.
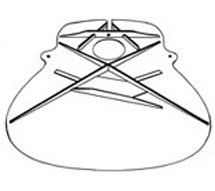
A-Frame X – Guitars in the X Series made with solid wood tops have wooden A-Frame X bracing. This system also has the same A-frame braces in combination with the Mortise & Tenon neck joint. But the bracing pattern has a slender, non-scalloped X brace with nice flexibility thanks to the long taper to the struts, which decreases in height as it moves away from the center of the X. Gone are the HPL support plates, and in their place are two thin support strips.
The unique bridge plate is set at an angle, closer to the sound hole on the bass side, and it is buttressed by one non-scalloped tone bar that is angled downward as it runs along the bridge plate. The X brace and tone bar create a “tone box” around the bridge plate, where the energy from the strings enters the soundboard.
Exception: X Series guitars made in the Grand Performance body size, like the GPC-X2E Macassar have the A-Frame X1 bracing, described below.
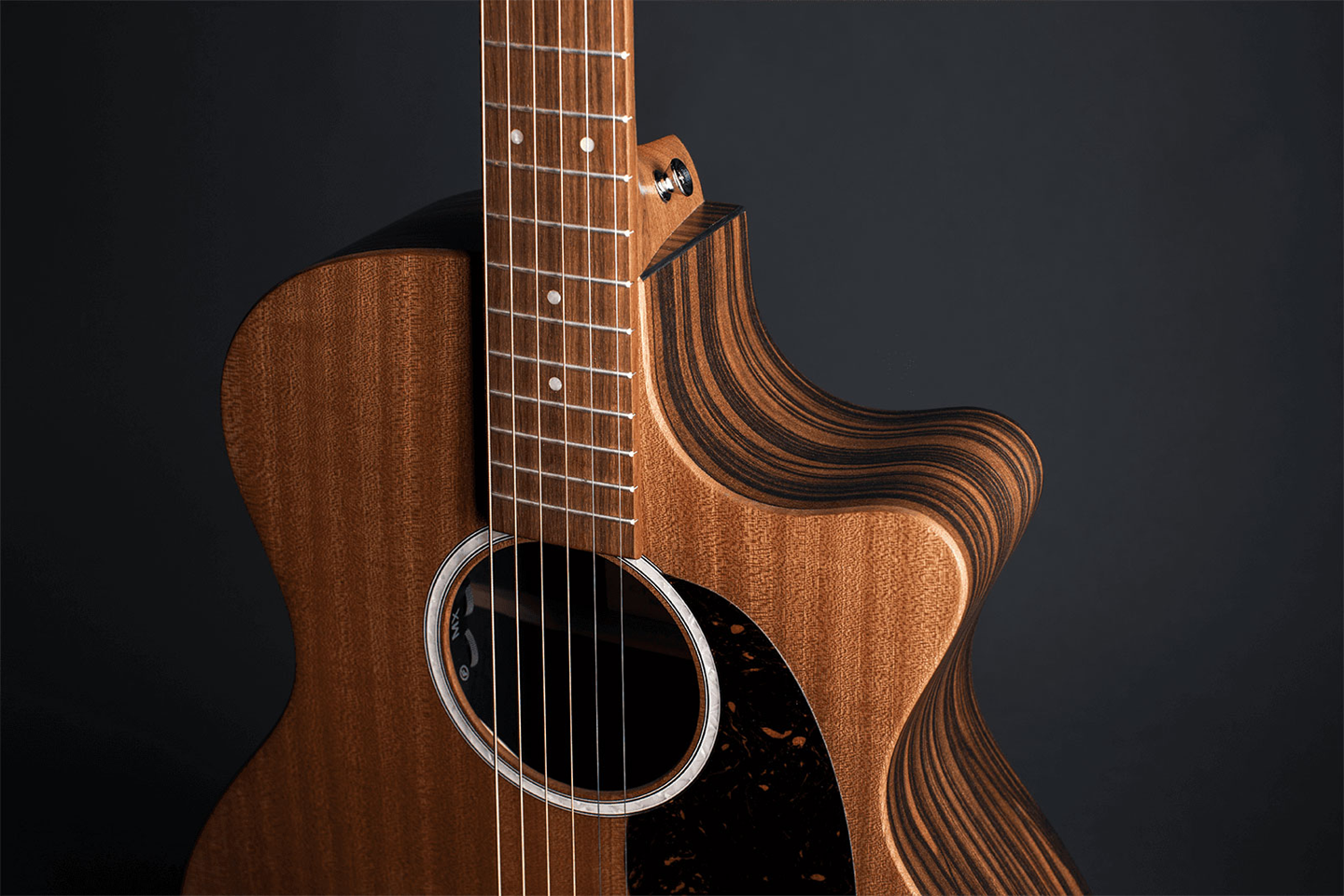
The GPC-X2E Macassar features a Sitka spruce top with A-Frame X1 bracing
Road Series Bracing
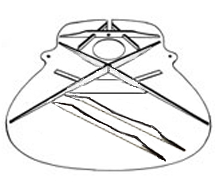
A-Frame X1 – The next advancement in Martin A-frame bracing, the “X1” pattern gets the same slender, X brace and radial support strips, now enhanced with two full-size tone bars below a traditional perpendicular bridge.
The tone bars are larger and longer than the solo bar used on A-Frame X bracing, and they are scalloped on all current models with this bracing pattern. The tips of the bars connect to the bass side strut of the X brace, slanting down and across the full expanse of the lower bout, helping to disseminate tone-producing energy across the center of the soundboard where the greatest portion of classic Martin tone is created.
EXCEPTION: The new SC-13E is Martin’s first 13-fret guitar, and has patented Tone Tension bracing, designed expressly for its unique asymmetrical body size and revolutionary Linear Dovetail neck joint. Each brace and bar has a radiused bottom to add tension to the soundboard. (See below for more information about radiused braces.)
Note: A-Frame X1 bracing was mislabeled as “Hybrid-X bracing” in the 2020 edition of Martin: Journal of the Acoustic Guitar. Hybrid-X bracing was entirely different, and appeared in the 1990s on higher-end models that employed the M&T neck joint. It ceased to exist with the introduction of the Simple Dovetail neck joint.
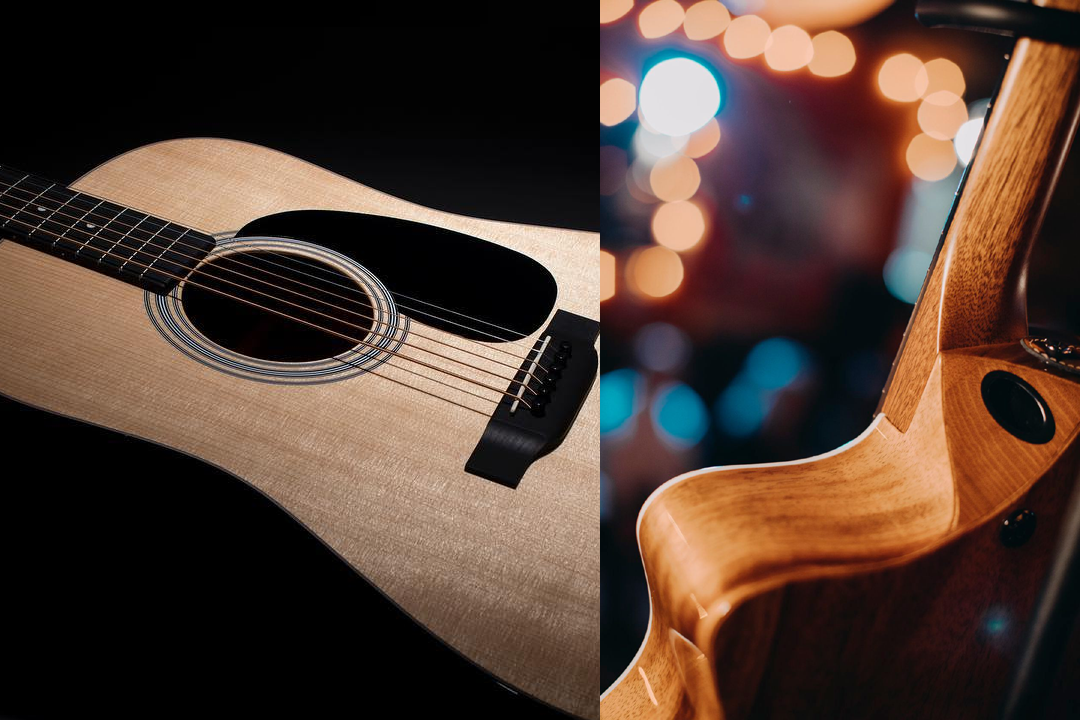
The D-12E has the double scalloped tone bars of A-Frame X1 bracing, the SC-13E has radiused bracing to go along with its asymmetrical body shape and revolutionary heel-less neck joint.
15 Series Bracing
Guitars in the 15 Series feature A-Frame X bracing, even though they are now made with the Simple Dovetail neck joint. The extra-responsive bracing in this pattern works so well with the hardwood mahogany top that Martin has been hesitant to mess with a good thing.
Exception: The new DSS-15M StreetMaster, with its extra-large sloped shoulder top, is made with Standard Bracing (see below.)
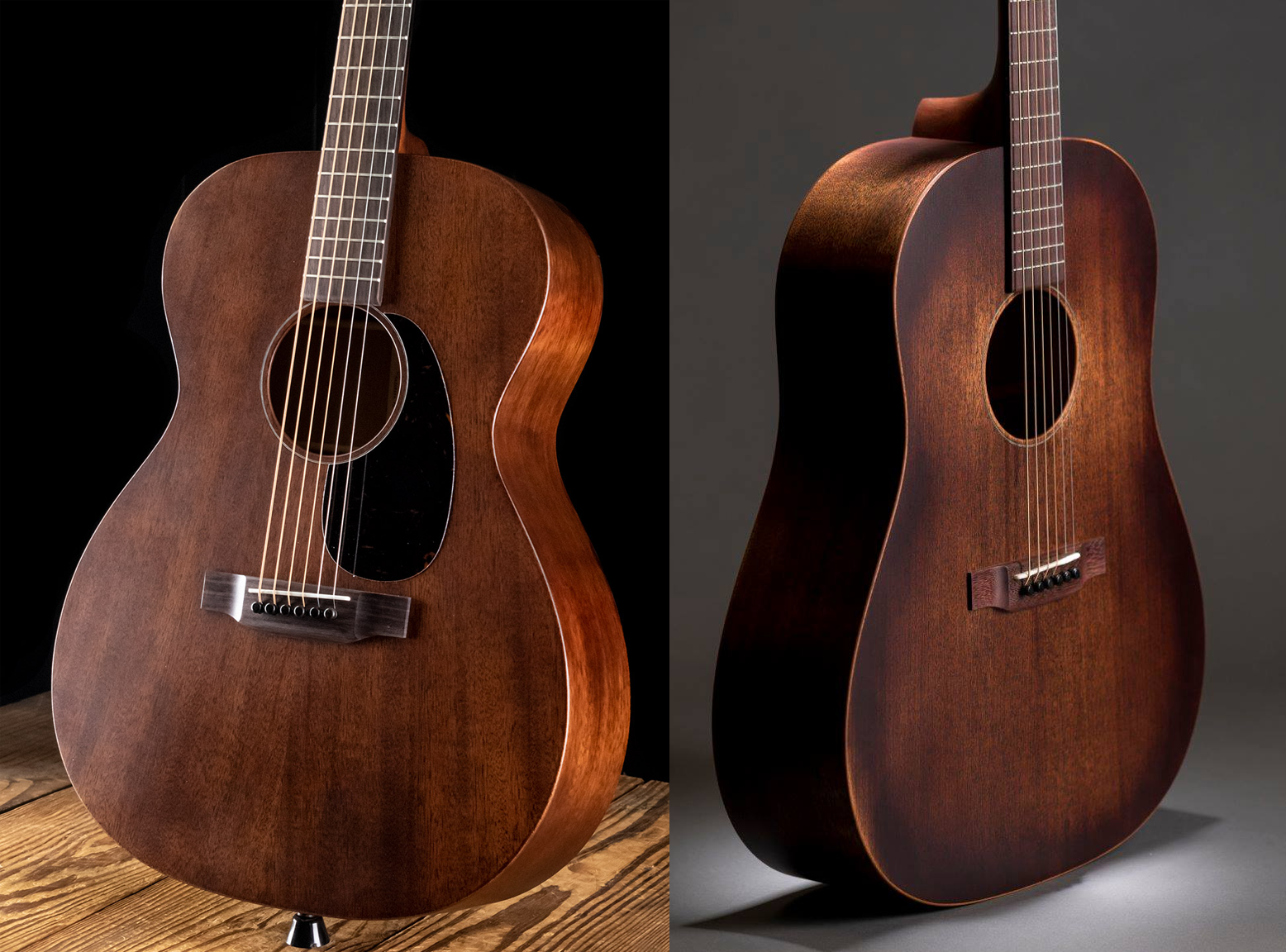
The 000-15M Natural has ultra-responsive A-Frame X bracing, the large and powerful DSS-15M StreetMaster makes the most of its forward-shift scalloped bracing
Standard Bracing
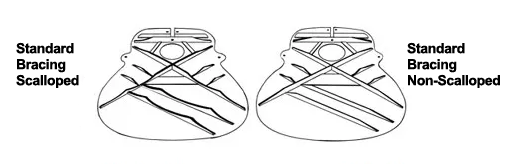
Scalloped and Non-Scalloped Bracing on display for the Martin Factory tour
The 15 Series is where A-Frame Bracing ends and Standard Bracing begins. Standard Bracing is used on all other models constructed at Martin’s main facility in Nazareth, PA. The bracing is named for the Standard Series, where it evolved. It is the direct descendent of the scalloped X-bracing invented by C. F. Martin Sr. in the middle of the nineteenth century.
Guitars made with A-Frame Bracing have flat bottom braces. All of the braces and tone bars used in Standard Bracing have a radiused bottom, meaning that the surface that gets glued to the soundboard has a subtle curve shaped into it. This gives each brace or bar an inherent amount of pull when it is glued down flat, and collectively adds permanent tension to the overall soundboard. They help to create the barely perceptible radius to what is a “flat top” guitar in name only.
Unlike bracing created for guitars featuring the Mortis & Tenon neck joint, Standard Bracing does not use the A-frame braces above the sound hole, because the traditional Compound Dovetail neck joint and the modern Simple Dovetail neck joint do not require them.
Instead, the shoulders and fretboard extension are supported by a wide shallow brace with a curved shape, called the “top plate,” positioned above the #1 brace. The area on either side of the X brace has two “radial braces” that are thicker than the flat strips used with A-Frame bracing, and which are carved in a manner similar to the tone bars and X brace. But three flat strips are used to surround the edge of the sound hole, known as “sound hole braces.”
Below the bridge plate are two full-sized tone bars. (Three tone bars being used for the Grand Jumbo body size.) The X brace and tone bars are larger than those used in the Road and X Series, and are more intricately shaped after they have been glued to the soundboard with a vacuum seal. Scallops are carved by a specially-trained artisan using a chisel, with the ends of the braces likewise being tapered and feathered by the hand.
Except for two models in the Standard Series, Standard Bracing includes a scalloped X brace and tone bars on all models, with similar shaping to the radial braces. The details of how the braces are shaped and exactly where they are laid out can differ, based on the specific body size, within a particular series.
In general, Martins with Standard Bracing have a 5/16” width to the X brace and tone bars on any top larger than size 00 (and 00L.) But there are exceptions, as the D-35, HD-35, 000-18, and all OM models, have 1/4" top bracing, as do all guitars made in sizes 0 and 00. And the OM-28 Authentic 1931 combines a 5/16” X brace with 1/4" tone bars and radial braces. If there is a rule in place, Martin will find somewhere to break it.
16 Series Bracing
The main models in the 16 Series all have Standard Bracing. The D and GPC models have scalloped, forward-shifted bracing. The Grand J-16E has forward-shifted bracing unique to the Grand Jumbo design, with a tapered X brace and three progressively-scalloped tone bars, meaning the first has no scalloping, the second has some scalloping, and the third has a lot of scalloping.
The only Martin guitar currently in production that uses nylon strings is the 00C12-16E Nylon. It has a special X bracing pattern inspired by the Martin guitars from before the steel-string era, when they were the first choice for virtuosi of the Classical repertoire.
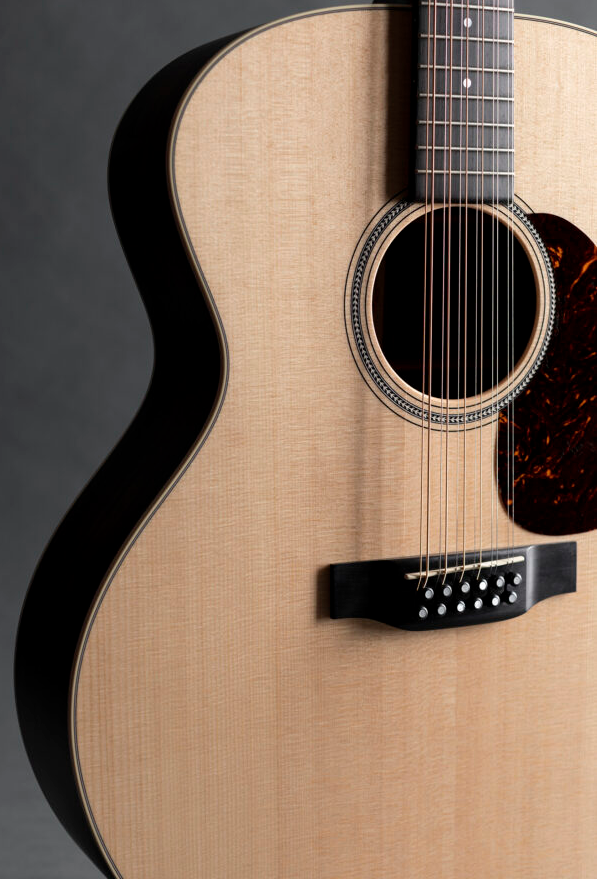
The Grand J-16E 12-string has a bracing pattern unique to the Grand Jumbo size
17 Series Bracing
The 17 Series currently offers two body sizes, both with Standard Bracing. The slope shoulder DSS-17 Black Smoke and DSS-17 Whiskey Sunset have forward-shifted, scalloped braces. The traditional short-scale 000-17 Black Smoke and 000-17 Whiskey Sunset have scalloped braces and a smaller bridge plate than is used on other 000s, which, along with its thin one-coat satin finish helps achieve its unique Depression Era tone.
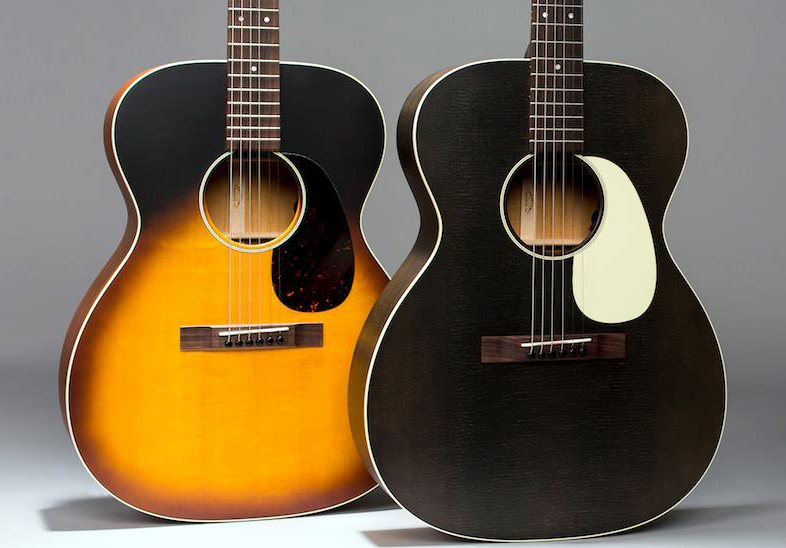
The 000-17’s extra-small bridge plate makes it extra responsive
Standard Series Bracing
Built with all-solid tonewoods, including Genuine Mahogany back and sides for the Style 18 guitars and with East Indian rosewood for guitars built in Style 21 through Style 45, the Standard Series sets the world’s standard that all other professional-level acoustic guitars must try to emulate. Today’s Standard Bracing is a big part of their magnificent Martin tone.
All Standard Series Martins with a top larger than size 000/OM have forward-shifted bracing. All Standard Series guitars have hand-shaped scalloped bracing, with the important exception of two iconic Martin models, the D-28 and the D-35. These are the only two Standard Series Martins made today with non-scalloped braces.
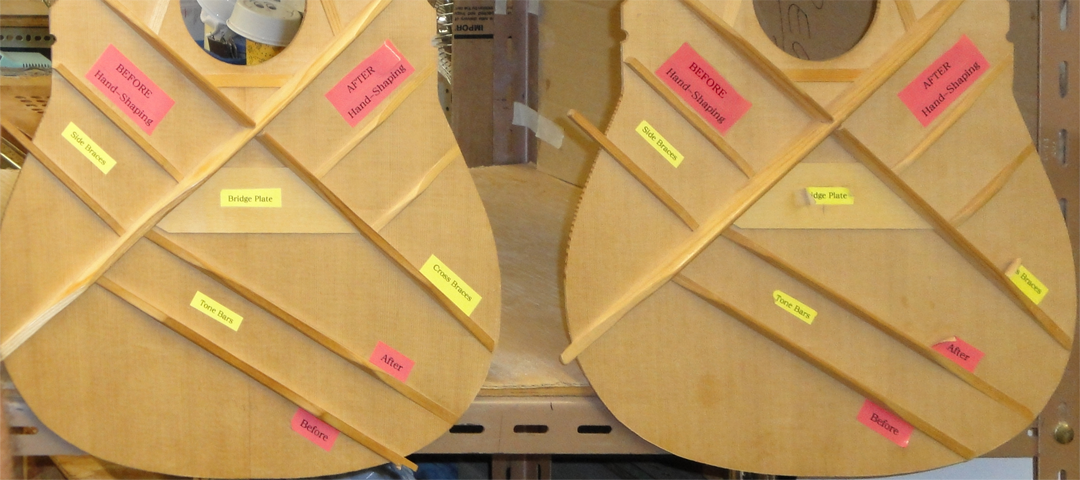
The signature sound of non-scalloped bracing is heard in the strong fundamental notes with exceptional string to string definition. There is considerable clarity and separation between the sound of the each string, with the main notes of a chord or picking pattern standing out beyond the radiating body resonance, and standing up to the hardest strumming with the thickest pick.
The D-28, with non-scalloped 5/16” braces, has solid, fat notes with remain focused and defined from the highest harmonic to the lowest bass tones. The D-35, with non-scalloped 1/4" braces, has precise and punchy treble notes by comparison, and a signature throb from a rounder, fuller bass.
Each model has its close counterpart made with scalloped-braces, the HD-28 and HD-35, recognizable by their herringbone top trim. These equally popular guitars have a reverberative body resonance that swells out and embraces the fundamental notes, for even richer voices that are often referred to as sounding lush or more complex.
This does not mean the HD-28 and HD-35 do not have definition or that the D-28 and D-35 do not have complex body resonance. But it is a matter of a degree as to how much of each they possess and provide the guitarist. And it is very much a matter of personal choice when it comes to how much definition and how much resonance you prefer.
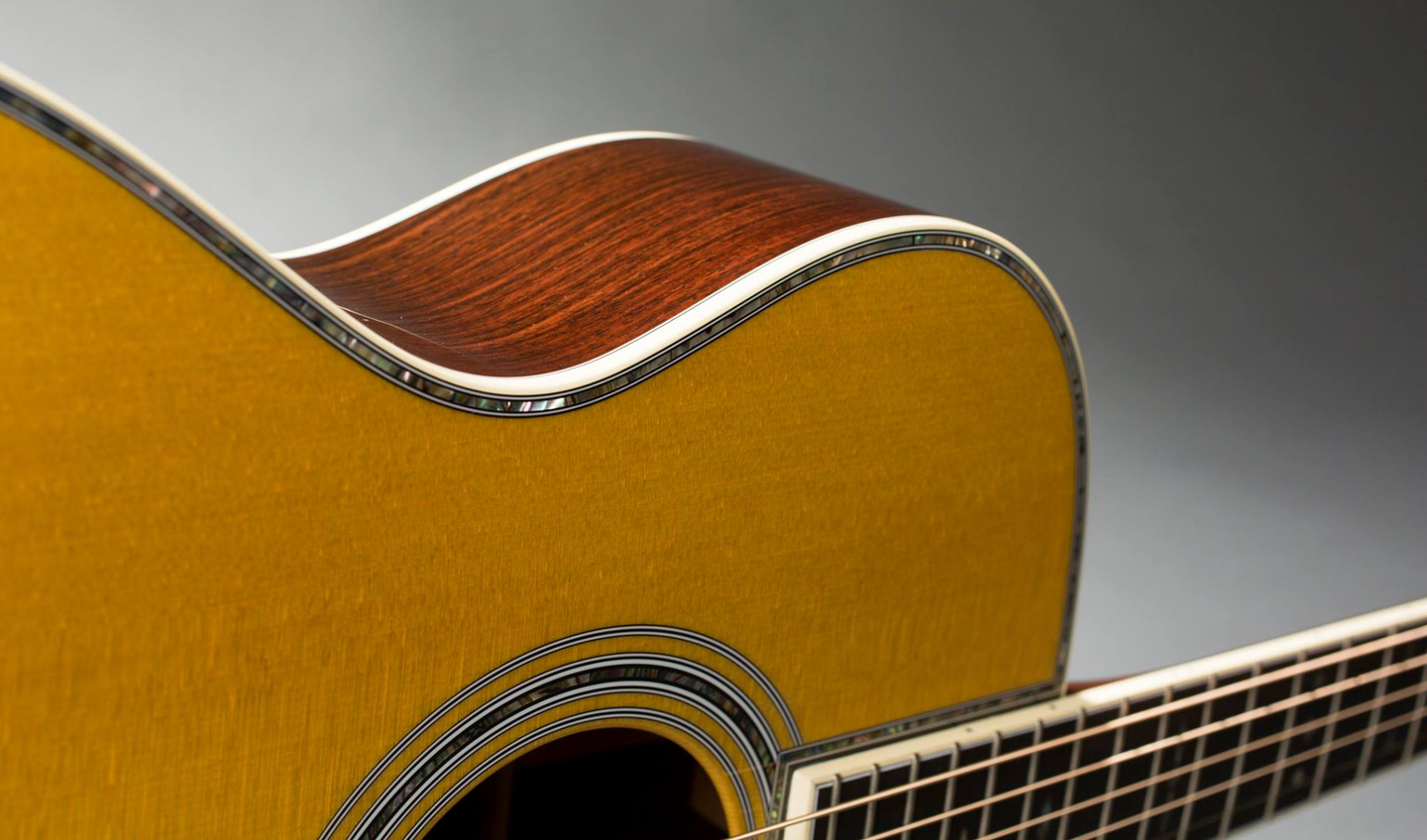
The opulent OM-42 achieves its perfect tonal balance via 1/4" scalloped bracing
Modern Deluxe Series Bracing
To go along with their many special features, the Modern Deluxe models have Standard Bracing with “Golden Era” scalloping. This technique uses longer, deeper scallops to remove more wood from braces made from Adirondack spruce, which has greater cross-grain stiffness than the Sitka spruce used for most Martin bracing. Basically, the tops and sides of Modern Deluxe Series braces are shaped more like braces used at Martin in the 1930s.
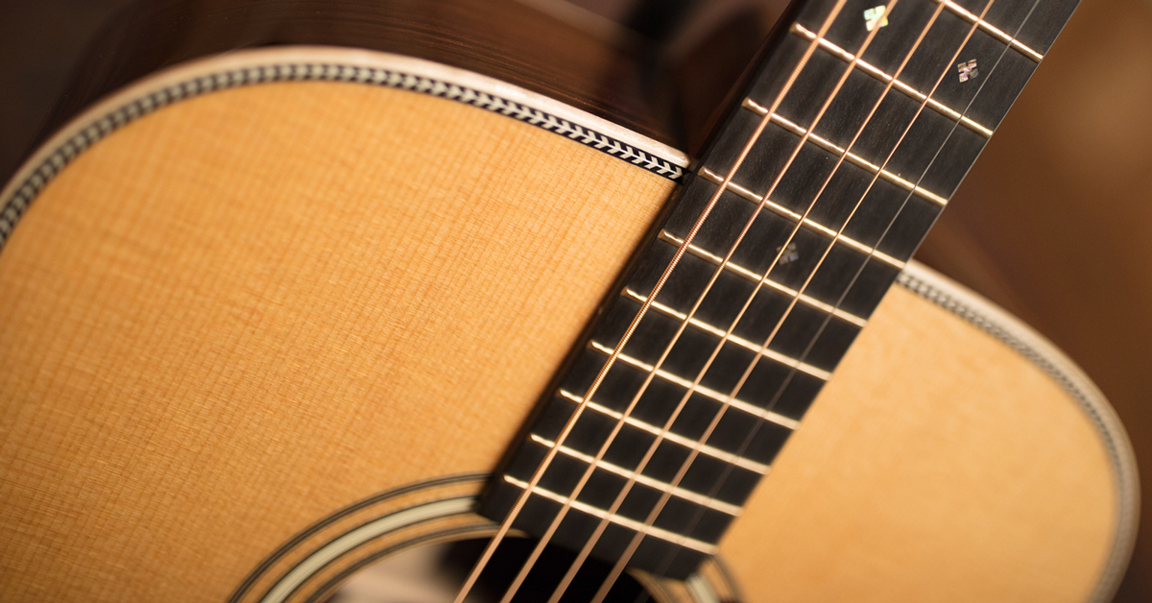
The elite D-28 Modern Deluxe has Golden Era scalloped braces
Authentic Series Bracing
The Authentic Series consists of elite models, each a close replication of one specific vintage Martin guitar that has survived in all-original condition. The main differences between Authentic Series bracing and Standard Bracing has to do with a technique known as “tucking.”
On an Authentic Series guitar the bridge plate is longer than on Standard Bracing patterns. Instead of fitting up against the X brace, a notch is carved into the underside of each X brace strut so the bridge plate ends tuck underneath it, creating more surface area connection for the transference of energy passing from the strings through the bridge plate to the X brace.
Likewise, the ends of the tone bars are tucked under the X brace, and the ends of the X brace are tucked into the cedar kerfing glued to the side, where the edges of the soundboard rest. This painstaking network of tucked bracing is all achieved by expert luthiers in Martin’s Custom Shop, to replicate the vintage tone of a pre-war Martin.
The shaping of the braces is also different. The entire brace is carved all the way around, from the scalloping at the top to the radius at the back. This carving is unique to each Authentic Series model, since even tiny details in the braces and bridge plates of the specific vintage Martin are noted and then recreated as closely as possible on its modern replica.
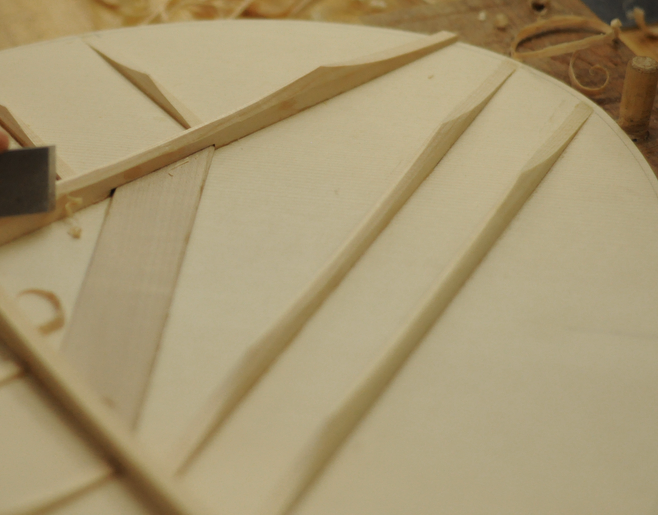
The Custom Shop luthiers are experts at vintage tucked bracing
Martin Guitar Bracing Conclusion
More musicians play or wish they could play a Martin than any other brand of guitar ever made. And Martin innovations like the bracing patterns created for their many original designs have a great deal to do with that.
Please let us know if you have any comments or questions about the information in this blog post, or if there is any further information you wish to know regarding Martin guitar bracing. We’d love to hear from you.
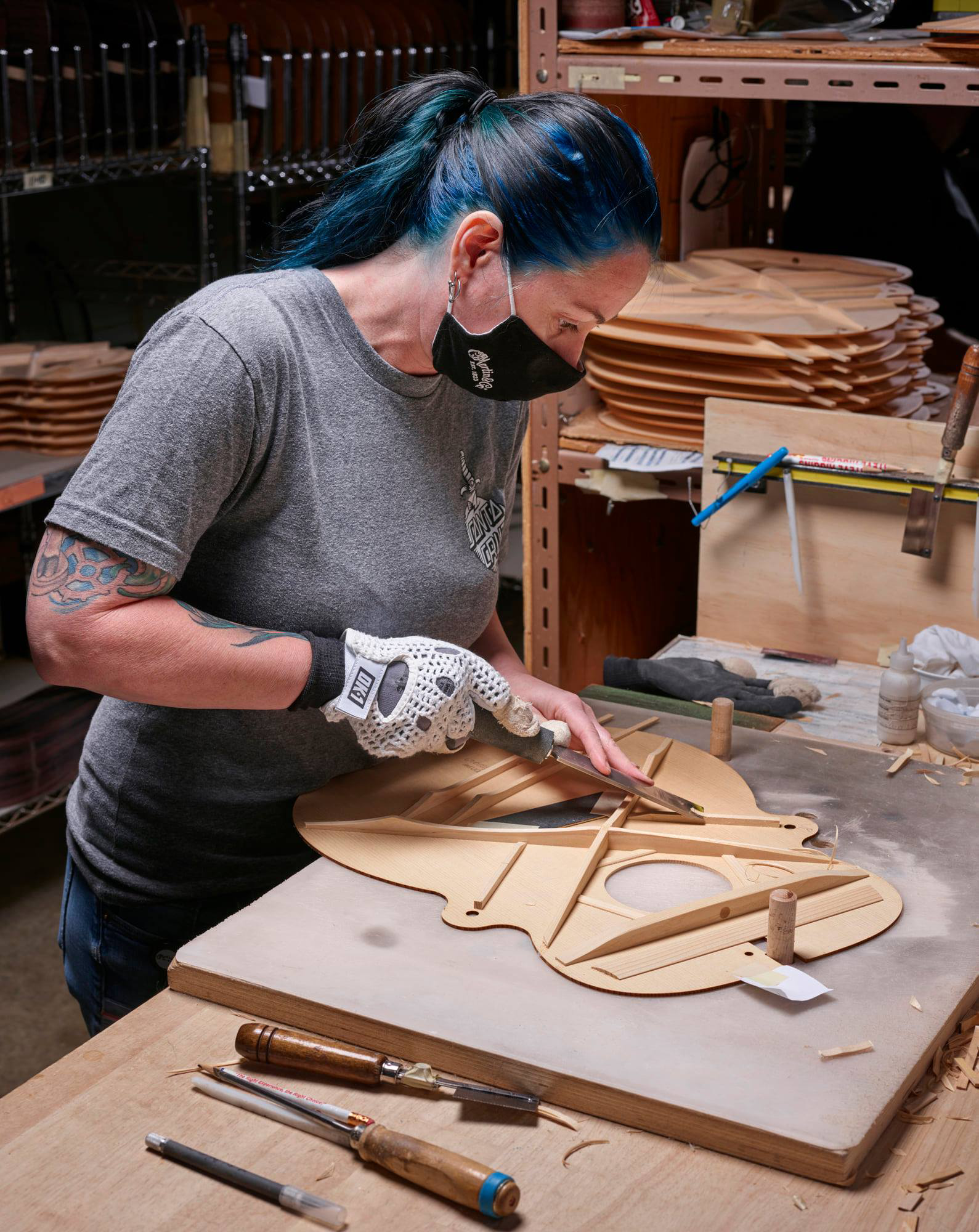
A Martin artisan scalloping braces for some lucky guitarist